Una tubería es el medio más popular para transportar materias primas ya que permite trasladar grandes volúmenes de fluidos en periodos relativamente cortos. Se estima que hay más de 3 500 000 km de tuberías en aproximadamente 120 países, de las cuales 65% se encuentran en Estados Unidos, 8% en Rusia y 3% en Canadá. Esto significa que los gobiernos y compañías que operan esta gran cantidad de tuberías dedican un esfuerzo colosal para gestionarlas de la manera más adecuada y prudente, lo que puede implicar diversas tareas de control, mantenimiento, optimización y diagnóstico1.
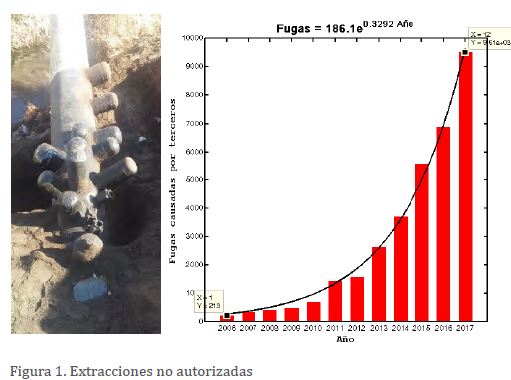
Desafortunadamente, a pesar de todas estas tareas enfocadas al buen funcionamiento de las redes de ductos y a la prevención de fallas, continúan presentándose eventos no deseados que provocan accidentes y daños irreversibles a la sociedad y al ambiente. Los eventos más comunes son las fugas causadas principalmente por el envejecimiento de las tuberías (corrosión), fallas en la instalación (particularmente en juntas y válvulas), eventos naturales (terremotos, huracanes y tsunamis), la humedad, las extracciones ilegales y los sabotajes terroristas. Sólo en Estados Unidos entre 1997 y 2016 se produjeron 832 accidentes graves en redes de distribución de gas, que causaron 310 muertes y 1299 heridos, además de la pérdida de millones de dólares en daños materiales2. En México, muchos de los accidentes fueron consecuencia de fugas causadas por terceros o extracciones no autorizadas. En la figura 1 se muestra una gráfica del crecimiento exponencial de las extracciones no autorizadas desde 2006 hasta 2017. Haciendo una regresión no lineal con el número de extracciones año con año, se puede predecir que en 2018 se tendrán aproximadamente 13 439 extracciones no autorizadas si no se toman las medidas necesarias para detener su expansión3.
Por esta razón, la seguridad de las redes de ductos es una preocupación constante de los sectores involucrados, los cuales regulan formalmente el funcionamiento de las tuberías mediante normas oficiales para garantizar la seguridad de su operación, especialmente de las tuberías que transportan fluidos peligrosos. Además, estos sectores invierten generosos recursos para el desarrollo de nuevos sistemas de detección de fugas robustos y confiables.
De acuerdo a la norma API RP 1130, los sistemas de detección de fugas se clasifican en dos categorías: sistemas externos y sistemas internos. Los sistemas internos utilizan instrumentación de campo (por ejemplo, sensores de flujo, presión o de temperatura del fluido) para monitorear los parámetros internos de la tubería. Los sistemas externos utilizan radiómetros infrarrojos, cámaras térmicas, sensores de vapor, micrófonos acústicos o cables de fibra óptica para monitorear los parámetros externos de la tubería.
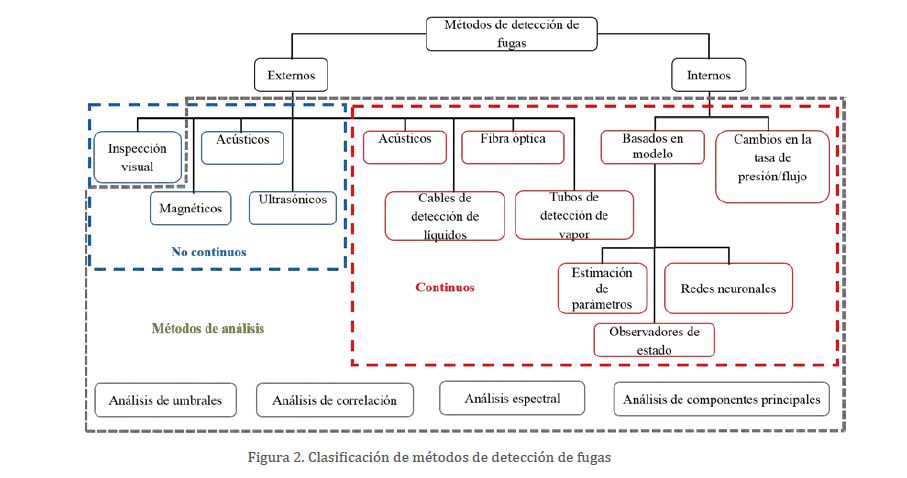
La figura 2 muestra un esquema de la clasificación de los métodos de detección de fugas. Hay que observar que éstos también pueden clasificarse en otras dos categorías: métodos continuos y no continuos. Los primeros son aquellos que monitorean continuamente la tubería conforme reciben información de los sensores. Los métodos no continuos son aquellos que se aplican una vez cada determinado periodo, diario, semanalmente o según el plan de diagnóstico y mantenimiento. En la práctica, los métodos continuos y no continuos a menudo se usan conjuntamente.
La mayoría de los métodos de detección de fugas desarrollados en el Instituto de Ingeniería de la UNAM por el grupo de Detección de Fallas son métodos basados en modelos, los cuales son muy populares entre los investigadores debido a su rentabilidad y eficiencia, aunque también gracias a los constantes avances tecnológicos en hardware, telecomunicaciones y al desarrollo de nuevas técnicas computacionales que permiten la implementación efectiva de estos métodos.
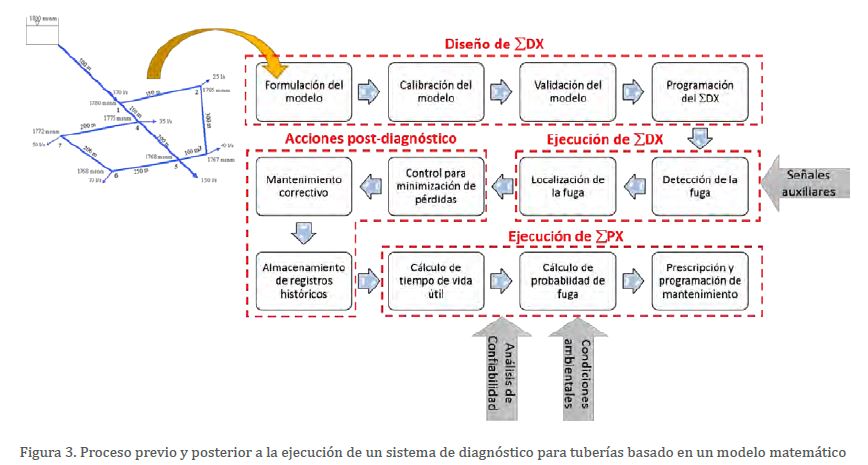
En la figura 3, se muestra un esquema del proceso general de la aplicación de un sistema de detección de fugas basado en un modelo desde su concepción hasta la posible ejecución de un sistema de pronóstico. Este proceso consta de cuatro etapas: 1. Diseño del sistema de diagnóstico (ΣDX). 2. Ejecución del sistema de diagnóstico. 3. Acciones postdiagnóstico y 4. Ejecución de un sistema de pronóstico. A su vez, cada una de estas etapas está conformada de sub-etapas que a continuación se describen.
Formulación del modelo. Algunos de los principios físicos utilizados para construir el modelo matemático de una tubería son los de conservación de masa, momento y energía. Las ecuaciones que describen estos principios son ecuaciones diferenciales parciales no lineales de tipo hiperbólico. Estas ecuaciones se pueden simplificar con base a ciertas suposiciones, por ejemplo, se pueden despreciar los términos convectivos o se pueden ignorar los cambios de densidad. También se pueden linealizar y aproximar como un conjunto de ecuaciones diferenciales ordinarias o algebro-diferenciales, incluso expresarse en función de la frecuencia. El tratamiento que se le dará al modelo dependerá de la técnica de diagnóstico que se empleará para detectar y localizar la fuga.
Calibración del modelo. Una vez formulado el modelo, necesitamos adecuarlo para que represente específicamente la tubería que se va a diagnosticar. Para ello necesitamos obtener los valores de los parámetros que utiliza el modelo. Estos pueden medirse directamente u obtenerse indirectamente a partir de las mediciones de gasto y presión utilizando técnicas de estimación de parámetros. Uno de los parámetros más difíciles de estimar es la fricción, que además debe estar bien calibrada pues los sistemas de diagnóstico son muy sensibles a ella. Un sistema de detección y localización con una fricción mal calibrada, producirá un diagnóstico erróneo.
Validación del modelo. Es el proceso de comprobar que los resultados aportados por el modelo para las variables de salida y de estado no son muy diferentes a los medidos en la realidad. Existen diferentes índices que permiten cuantificar el grado de ajuste entre los datos medidos y los resultados del modelo, por ejemplo, el RSME/MAE (cociente entre el error cuadrático medio y el error absoluto medio) o el índice de ajuste modificado.
Programación del sistema de diagnóstico. En esta etapa el modelo se convierte en parte de un algoritmo de diagnóstico que se puede programar en una computadora o en una microcomputadora de bajo costo. Este algoritmo puede ser autónomo e independiente o ser parte de un sistema más complejo, como un sistema SCADA. Algunos de estos algoritmos están basados en técnicas de optimización, análisis de Fourier o control automático, como por ejemplo los observadores de estado.
Detección de la fuga. En esta primera sub-etapa de la ejecución del sistema de diagnóstico, la fuga es detectada ya sea calculando el balance de flujos de cada tubería supervisada o por un transitorio inusual de la presión. Algunos de los sistemas de diagnóstico más sofisticados descartan que el balance de flujos diferente de cero no sea producto de la descalibración de los sensores de flujo.
Localización de la fuga. En esta sub-etapa el sistema de diagnóstico proporciona la localización exacta de la fuga o el sector donde se encuentra. Tanto para la detección como para la localización se necesita, además del modelo, de las mediciones del flujo y de presión debidamente procesadas. Algunos sistemas de diagnóstico sofisticados, envían señales de presión a la tubería para perturbar el fluido y obtener más información que ayude al diagnóstico.
Control de minimización de pérdidas. Una de las primeras acciones a realizar después del diagnóstico es minimizar las pérdidas del fluido cerrando las válvulas necesarias para aislar el sector del ducto con fuga, o en caso de que esto no sea posible, bajar el diferencial de presión para reducir el flujo en el ducto y por consecuencia el flujo de la fuga.
Mantenimiento correctivo y análisis de fallas. Las fugas son reparadas o el ducto reemplazado, según la severidad del problema. Además, se colectan los elementos necesarios para determinar el origen de la falla.
Almacenamiento de registros históricos. El almacenamiento de los resultados del diagnóstico, las señales producidas durante la fuga, el origen de la fuga, la frecuencia de la aparición de fugas por año y las estadísticas de los daños causados, permiten poseer la información necesaria para alimentar un sistema de predicción que permita pronosticar posibles fugas en un determinado periodo.
Cálculo de vida útil. Es el tiempo que le queda de servicio a la tubería en un momento particular de su operación. Su estimación es fundamental para su mantenimiento y para calcular las probabilidades de fuga. La vida útil es aleatoria y desconocida, y como tal debe estimarse a partir de registros históricos, de un análisis de confiabilidad y de las condiciones ambientales a las que está expuesta la tubería.
Cálculo de probabilidad de fuga. En esta etapa se estima el riesgo de fugas en un determinado periodo con base a los registros históricos y al cálculo de vida útil.
Prescripción y programación de mantenimiento. Con base a la información del diagnóstico y pronóstico, se pueden programar las actividades de mantenimiento preventivo con la finalidad de extender la vida útil de la tubería.
Referencias
1 Factbook, C. I. A. (2010). The World Factbook.
https://www.cia.gov/library/publications/the-world-factbook/
fields/2117.html.
2 U.S. Department of Transportation (2016). Pipeline and Hazardous Materials Safety Administration: Serious Pipeline Incidents Report.
3 Pemex (2018). Reporte de Tomas Clandestinas. http://www.pemex.com/ acerca/informes_publicaciones/Paginas/tomas-clandestinas.aspx