Geotecnia y Aspectos constructivos del túnel de la Línea 12 del metro
Ismail Benamar
Ex-gerente de construcción en ICA–Construcción Especializada
Introducción
La finalidad de construir gran parte del tramo poniente de la línea 12 del Metro en túnel fue minimizar las afectaciones en superficie de una zona de la ciudad densamente poblada y con presencia de algunos de los ejes de vialidad más transitados.
En la zona de los últimos 900 m al extremo poniente de la línea, el terreno es competente; no hay presencia de agua freática a nivel del trazado de la línea, y este tramo, al situarse al poniente de la estación terminal Mixcoac, tiene una sección con geometría en forma de herradura ancha para la instalación de varias vías de estacionamiento de los trenes, lo que permitió su ejecución con un método convencional (NATM) sin problemas.
La otra parte en túnel, con longitud de 7.7 km, transcurre en suelos blandos bajo nivel freático. Estos suelos varían, en el sentido oriente-poniente, desde suelos arcillosos blandos con alto contenido de agua y alta compresibilidad, hasta suelos limoarenosos compactos, e incluso con presencia de gravas y boleos. El método de excavación elegido fue con una tuneladora de presión de tierra balanceada (EPB–Earth Pressure Balanced) que permite equilibrar las presiones del terreno en el frente de excavación por medio de la presión que mantiene el material excavado dentro de la cámara de excavación de la tuneladora, y de esta forma minimizar las perturbaciones a las estructuras enterradas o superficiales cercanas al túnel.
El túnel con tuneladora tiene una diámetro excavado de 10.20 m y un diámetro terminado revestido de 9.11 m. El revestimiento está compuesto por anillos de dovelas prefabricadas de concreto armado, con espesor de 40 cm (7 dovelas + 1 cuña/anillo).
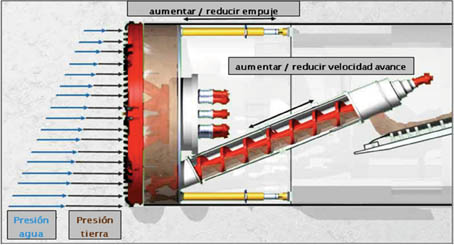
Figura 1. Principio de funcionamiento de una tuneladora tipo EPB
El objetivo del presente artículo relacionado con el túnel hecho con tuneladora de la línea 12 es presentar el contexto geotécnico en el cual se ha desarrollado la excavación del túnel, las particularidades de la tuneladora seleccionada, el procedimiento de montaje y la excavación con la tuneladora que le permite avanzar en los terrenos presentes con baja cobertura sin afectar las estructuras cercanas, y finalmente la instrumentación geotécnica llevada a cabo para el control del procedimiento de excavación.
Contexto geotécnico
En su parte inicial, el túnel se encuentra con una estratigrafía compuesta principalmente por suelos blandos arcillosos con altos contenidos de agua (hasta más del 300 %), alta plasticidad y baja resistencia intercalados por lentes de arena y ceniza volcánica. Por encima de estas arcillas blandas se encuentra un estrato de arcilla arenosa de consistencia firme, y más arriba la costra o relleno superficial de materiales arenolimosos. Bajo el estrato arcilloso en el que corre el túnel se encuentran los depósitos profundos de limos arenosos y arenas con gravas aisladas.
Al avanzar hacia el poniente, el túnel se va introduciendo en los depósitos profundos de arenas limosas, limos arenosos y arenas con gravas aisladas. En el tramo intermedio del túnel, el perfil ascendente de los depósitos profundos hace que el túnel se encuentre empotrado en su parte inferior en estos depósitos más duros. Hacia el final del trazo, el túnel fue en su totalidad excavado en los limos y las arenas de la zona de Lomas, y en su paso se encontraron boleos.
Es importante mencionar que los estratos arcillosos en los que se desarrolla el túnel en su tramo inicial están sujetos, como el resto del subsuelo arcilloso de la ciudad de México, a la consolidación regional por la extracción de agua. Dentro de la información recabada durante la campaña de investigación geotécnica se encontró el nivel de aguas freáticas entre 2 y 3 m de profundidad. De este nivel y hasta profundidades de alrededor de 11 a 15 m, la distribución piezométrica es la hidrostática. A profundidades mayores, las curvas piezométricas mostraron abatimiento hasta alcanzar los depósitos profundos donde la presión intersticial es prácticamente nula. El perfil estratigráfico del túnel se muestra en la figura 2.
Con el perfil estratigráfico del túnel establecido y los datos geotécnicos de los diferentes estratos se realizaron cálculos previos al inicio de la excavación para estimar los valores de presión frontal a aplicar durante la fase de excavación con la tuneladora EPB y los asentamientos máximos previsibles en superficie (Attewell et al., 1982; Kolymbas, 2008).
Por otro lado, dada la heterogeneidad, en el sentido longitudinal, de los terrenos atravesados por la tuneladora, y para optimizar el diseño del revestimiento del túnel a base de dovelas de concreto armado, se ha dividido el trazo del túnel en 5 zonas geotécnicamente homogéneas. Se ha elaborado un diseño estructural del revestimiento distinto en cada zona (sin cambio de geometría).
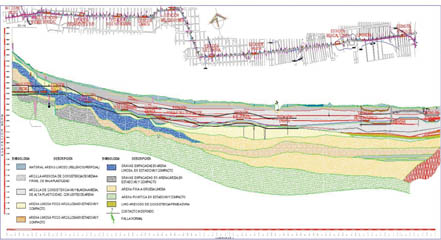
Figura 2. Perfil estratigráfico del túnel de la línea 12
Características de la tuneladora
El túnel de la línea 12 transcurre en un medio urbano en suelos blandos bajo nivel freático; por lo tanto, el uso de una tuneladora con frente presurizado se imponía. En este caso, dos tipos de tuneladoras se pueden usar: con presión de tierra (EPB) o con presión de lodos (Slurryshield). En los terrenos que atraviesa el túnel predominan los finos, y en este caso se recomienda el uso de una tuneladora tipo EPB, según se puede deducir de la gráfica de la figura 3. En la parte final del túnel, hacia el oeste, predominan los terrenos granulares, pero la tuneladora EPB puede lidiar con estos terrenos mediante el uso de aditivos condicionantes del terreno.
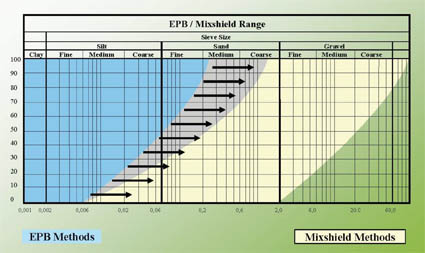
Figura 3. Gráfica de campo de aplicación de tuneladoras EPB y Slurryshield
Una vez definido el tipo de tuneladora (EPB), se trabaja de la mano con el proveedor de la tuneladora para considerar las opciones adicionales que debe llevar la máquina para adecuarla a las condiciones de la obra. En este caso, se consideran para su estudio parámetros como la longitud total por excavar, las dimensiones de las lumbreras de inicio y de salida, el diámetro de excavación como función del gálibo funcional del túnel, el método de retiro de rezaga, las características geométricas del alineamiento del túnel (pendientes y curvas), etc. Las principales características geométricas y físicas de la tuneladora seleccionada están resumidas en la tabla 1.
Tabla 1. Principales características de la tuneladora
Diámetro de excavación |
10.20 m |
Diámetro interior del revestimiento |
9.11 m |
Longitud total escudo + back up |
108 m |
Empuje máximo |
8400 t |
Torque máximo |
20 300 kN.m |
Potencia eléctrica instalada |
5000 kVA |
Capacidad de retiro de rezaga |
360 m3/h |
Peso total |
1100 t |
Un requisito importante en este túnel, excavado en medio urbano denso con gran diámetro en suelos blandos y con baja cobertura, es minimizar los asentamientos en superficie y las interacciones con las estructuras vecinas enterradas o en superficie. Para su cumplimiento se ha decidido usar la inyección de relleno anular (entre el terreno excavado y el revestimiento de dovelas) atrás de la tuneladora mediante bicomponente. Es una técnica muy utilizada en Japón, pero poco común en el resto del mundo al momento que fue pedida esta tuneladora (a finales de 2008). Últimamente estamos viendo que su uso se está generalizando.
El bicomponente es una mezcla de dos líquidos:
Líquido A: lechada, que a su vez es una mezcla de agua, bentonita y cemento.
Líquido B: aditivo acelerante.
Los líquidos A y B están almacenados en dos tanques distintos en el back up de la tuneladora y se inyectan a través de dos circuitos paralelos e independientes. Los dos líquidos se mezclan únicamente en la parte final del sistema de inyección justo antes de llegar al espacio anular. Al momento que se mezclan, el líquido B actúa sobre el líquido A para generar una masa gelatinosa en cuestión de segundos, y en algunos minutos se inicia el fraguado de la mezcla (ver figura 4).
Figura 4. Curva de inicio de fraguado de la mezcla bicomponente
Con su fraguado rápido en el terreno, el uso del bicomponente en los terrenos muy blandos con capacidad nula de autosoporte, como el caso de las arcillas blandas de la ciudad de México, nos ha permitido mantener los asentamientos en superficie en rangos controlables que no han afectado las estructuras vecinas.
Ensamble de la tuneladora e inicio de la excavación
El proceso de excavación del túnel de la línea 12 se inició con el ensamble de la tuneladora en el sitio de la obra. Comúnmente se lleva a cabo un preensamble y pruebas de las tuneladoras en la planta de fabricación del proveedor previamente a su envío a la obra y posteriormente a su ensamble definitivo. En el caso de la tuneladora de la línea 12, se llevó a cabo el primer ensamble de la tuneladora directamente en el sitio de obra en un proceso llamado On-site First Time Assembly (OFTA). El proceso OFTA fue convenido con el proveedor desde la fase de pedido de la tuneladora para reducir el plazo de entrega de sus componentes al sitio de la obra. El proceso completo de montaje y prueba de la tuneladora en el sitio de la obra tardó 2.5 meses, que se considera dentro del promedio de tiempos de ensamble de tuneladoras similares. Esto significa que el ahorro en tiempo que ha aportado el proceso OFTA es real y puede considerarse en otros proyectos similares.
Figura 5. Proceso de ensamble de la tuneladora
La lumbrera de ensamble de la tuneladora está situada entre las estaciones Atlalilco y Mexicaltzingo. Esta lumbrera fue ejecutada mediante pantallas preexcavadas de concreto armado (muros Milán). Es rectangular, de 34 m de largo, 14 m de ancho y 17 m de profundidad. Se ha optimizado su diseño para poder disponer de la máxima área libre para el ensamble del escudo. Esta lumbrera ha permitido el ensamble en su fondo del escudo y del primer remolque del back up que contiene en particular el segundo tornillo sin fin, la cabina de operación de la tuneladora y las unidades hidráulicas. El resto de los remolques del back up (6 remolques) fueron ensamblados en superficie y conectados al escudo mediante “cordón umbilical”, constituido por una serie de mangueras hidráulicas y cables eléctricos que han permitido el inicio de la excavación con los 6 remolques del back up en superficie. A medida que avanzaba el escudo en el terreno, se podían bajar los remolques por pareja y seguir así avanzando hasta que se completó toda la tuneladora dentro del túnel.
Antes de iniciar la excavación se ha realizado un mejoramiento del terreno detrás del muro de ataque de la lumbrera de ensamble, lo que ha permitido demoler la sección equivalente a la rueda de corte de la tuneladora en el muro de ataque sin riesgo de inestabilidad del terreno. También se ha colocado un doble sello circular sobre el muro de ataque y dentro del cual pasó la rueda de corte antes de iniciar la excavación del terreno.
El mejoramiento del terreno se ha realizado por sustitución del terreno de mala calidad mediante la ejecución de pilas de suelo-cemento. Este mejoramiento tiene la ventaja, en este caso, de ser fácil de ejecución y económico, y se coloca un terreno mejorado estable con resistencia final no muy alta (del orden de 3 MPa).
Este mejoramiento se ha ejecutado en la entrada y la salida de todas las estaciones subterráneas cruzadas por la tuneladora.
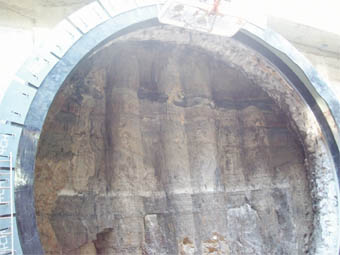
Figura 6. Vista del terreno mejorado
Instrumentación y monitoreo de la excavación
La instrumentación geotécnica es una parte muy importante dentro del proceso de excavación de un túnel, ya que permite verificar los efectos que la excavación está produciendo en el terreno, en superficie, en el mismo túnel y en las estructuras cercanas al túnel.
El túnel de la línea 12 se ha excavado en condiciones adversas: terreno excavado de muy mala calidad, por debajo del nivel freático, en zona urbana densa, gran diámetro de excavación con poca cobertura de terreno en el techo del túnel (entre 0.7 y 1.4 veces el diámetro de excavación), cruce de estructuras sensibles, etc. Por esta razón, se ha elaborado un extenso plan de instrumentación a lo largo del trazo del túnel, que incluye mediciones en superficie y en profundidad, en el terreno y en las estructuras potencialmente afectadas, incluido el propio túnel.
El plan de instrumentación se ha dividido en dos partes:
Instrumentación convencional a lo largo del trazo del túnel, que incluye referencias superficiales sobre el eje del túnel, referencias transversales al eje del túnel, medición de convergencias en el túnel, referencias en todas las fachadas de los edificios y casas alrededor del trazo del túnel, y medición de inclinación de todos los edificios de más de 3 pisos alrededor del trazo del túnel.
Instrumentación detallada enfocada a estructuras sensibles, y que incluye inclinómetros, extensómetros, piezómetros, piezoceldas, celdas de carga en las dovelas del revestimiento, medición de convergencia automatizada dentro del túnel e inclinómetros en las estructuras elevadas.
La instrumentación convencional nos permite llevar un control continuo durante la fase de excavación del túnel y poder corregir el procedimiento de excavación con la tuneladora en presencia de cualquier anomalía en los resultados de las mediciones llevadas a cabo. Esto supone una alimentación permanente y en tiempo de la información generada al equipo de ejecución del túnel para poder actuar, en su caso, de manera oportuna.
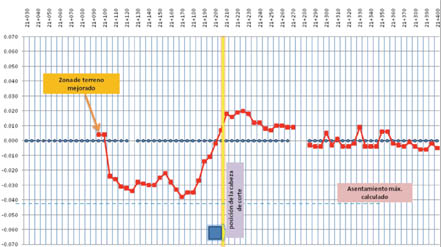
Figura 7. Ejemplo de curva de asentamientos sobre el eje del túnel (escala vertical en metros)
Todos los resultados de esta instrumentación han sido conformes a lo previsto en cada una de las zonas geotécnicas atravesadas por el túnel: los asentamientos máximos han sido iguales o menores a los calculados sin afectar las estructuras vecinas, y las convergencias dentro del túnel han sido limitadas a un máximo de 0.4 % del diámetro interior del túnel.
La instrumentación detallada ha sido instalada estratégicamente en las siguientes cinco secciones:
Iglesia San Marcos: paso del eje de la tuneladora a 10 m del borde de una iglesia del siglo XVI con cimentación superficial.
Cruce Churubusco: paso del túnel por un cruce bajo colector en funcionamiento de diámetro 4 m, bajo un río entubado y entre dos columnas de un puente vial con cimentación profunda a base de pilas. La distancia entre el techo del túnel y la base del colector es igual a 4 m. La distancia mínima entre el túnel y las pilas de los apoyos del puente es igual a 5 m.
Cruce Tlalpan: paso del túnel bajo la línea 2 del Metro, la cual es superficial en este tramo con una cobertura de terreno de apenas 8 m. El túnel cruzó también un paso deprimido vehicular con una cobertura de apenas 5 m.
Cruce Tokio: paso del túnel bajo casas de 1 a 3 niveles sin cimentación profunda y en un caso con un nivel de sótano. Paso del túnel a una distancia mínima de 60 cm de las pilas de cimentación de un edificio alto.
Cruce Zapata: paso del túnel bajo la línea 3 del Metro, la cual está en un cajón somero con una cobertura de 3 m.
A pesar de la complejidad de estos cruces, después de realizar análisis numéricos de interacción suelo-estructura para simular el paso de la tuneladora por estos cruces, se ha concluido que si se lleva un control riguroso de los parámetros de avance de la tuneladora, las deformaciones que iban a ser generadas no deberían ocasionar desperfectos a las estructuras vecinas en cada cruce. Y, por lo tanto, no era necesario llevar trabajos de refuerzo del terreno alrededor de estos cruces antes del paso de la tuneladora.
En cada caso, los instrumentos fueron instalados semanas antes del paso de la tuneladora, así como también las lecturas fueron verificadas y estabilizadas. En el caso de la instrumentación detallada, a excepción de los inclinómetros, los otros instrumentos miden de manera continua y con la frecuencia deseada los datos almacenados en un datalogger que a su vez era verificado y sus datos analizados hasta 4 veces por día.
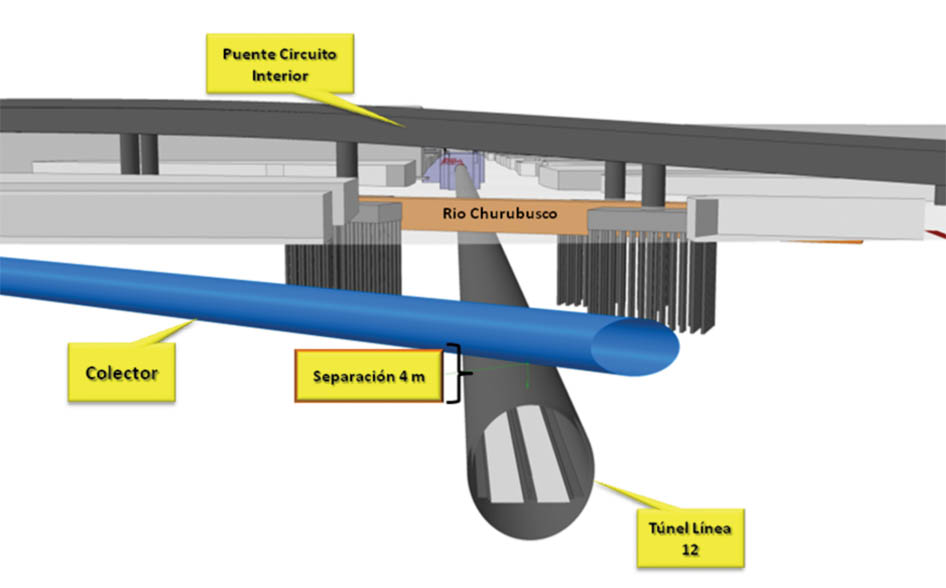
Figura 8. Configuración del cruce Churubusco
En las figuras 9a a 9c podemos ver las gráficas de los resultados de mediciones durante y después del paso de la tuneladora por el cruce Churubusco.
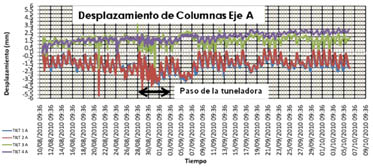
Figura 9a. Ubicación y mediciones de los inclinómetros
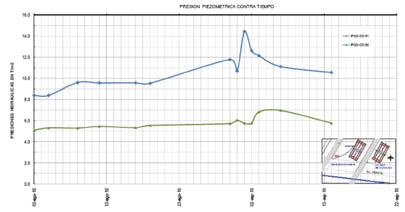
Figura 9b. Mediciones de los piezómetros
Se puede observar que las magnitudes de las deformaciones fueron limitadas y tendieron hacia la estabilidad rápidamente después del paso de la tuneladora. Al igual, para la presión piezométrica se ha notado un incremento temporal durante el paso de la tuneladora y después del paso se volvió a estabilizar a su valor anterior al paso. Esto demuestra también que el túnel es estanco y no actúa como un dren.
Lo anterior fue resultado de un estricto control de los parámetros de avance de la tuneladora, como la presión frontal, y el volumen y la presión de inyección de la mezcla bicomponente en el espacio anular entre terreno y revestimiento.
Este control se está realizando gracias a la disposición de una conexión que permite la visualización de todos los parámetros de avance de la tuneladora en tiempo real desde cualquier ordenador equipado de una conexión a Internet. Estos datos también se almacenan con una frecuencia seleccionada y se procesan diariamente para su posterior análisis.
Conclusiones
Para la excavación del túnel de la línea 12 se eligió el método de excavación con tuneladora tipo EPB a la cual se acondicionaron algunos complementos necesarios para llevar un mejor control de las deformaciones en las condiciones adversas de excavación de este túnel.
Con la instrumentación instalada fue posible medir en tiempo real los efectos de la excavación en el entorno. Los resultados muestran que el control de los parámetros de avance de la tuneladora fue el adecuado.
Es importante observar que los parámetros de avance se están llevando con base en valores calculados, y estos valores dependen de los datos geotécnicos del terreno obtenidos a partir de una extensa campaña geotécnica.
Referencias
* Attewell y Woodman (1982), Predicting the dynamics of ground settlement and its derivatives caused by tunneling in soil, Ground Engineering 15(8), pp. 13-22.
* Kolymbas (2008), Tunnelling and tunnel mechanics – a rational approach to tunnelling, Springer-Verlag Berlin Heidelberg, Alemania, pp. 331-336.